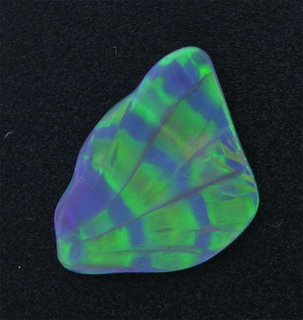
The Making Of A Masterpiece:
By Richard W. Wise, G.G.
©2006
Step 1: The Gem:
Recently a client fell in love with this unusual and fine black opal (left). Black opal is found at Lightning Ridge in New South Wales, Australia and almost nowhere else. The cutter, Christine Roussel, noting the unusual color pattern in the stone cut it to resemble a butterfly’s wing. We all agreed that the best use of the gem would be to make a butterfly piece, in this case a pendant for his wife. A combination brooch/pendant would have added flexible but as his wife never wears pins he decided against a combination piece. Few people have ever seen the steps necessary to produce a fine handmade original so we decided to document the making of this masterpiece.
Step 2: The Concept:
Goldsmiths often rely upon a particular gemstone to stimulate the creative juices. In this case, our chief designer, Douglas Canivet executed a number of sketches or studies for our client. Once the client approved the concept, we decided to make a full color rendering to give us the flavor of the finished piece. For dimensionality it was decided to execute it using the ancient repoussé technique. The French word means literally “to work from the back”. The result is a bas-relief when the piece is viewed right side up. The client decided that the body and wing of the butterfly would be executed in a combination of 18k yellow and rose gold. For contrast and strength, the antenna and feet would be made in platinum wire.
Step 3: Execution:
To render a concept is one thing to execute it is quite another. First, a template is made and each of the components is cut out with a jeweler’s saw. Rose appliqués are applied to wing and the wing and body components are pressed into an iron bowl filled with warm pitch. Once cooled, the pitch holds and provides a flexible cushion for the metal. . Set in pitch steel punches can be used to sculpt and expand the metal. Although gold is the most plastic of metals, the cushioning effect of the pitch is necessary to prevent the steel tool from
slicing through or cracking the gold.
A bezel is made to hold the gem. The bezel is simple speaking a box made to hold the stone. It must conform exactly to the shape of the stone (no easy task with a wing shaped stone). Later, the edge of the metal is pressed up against the gem to hold it securely in place. Pictured (left) is the finished body, wing and bezel. Note the rose colored spots in the wing shape, the result of the shaped pieces of rose that was applied to the yellow gold. Repousse work also produces a beautiful textured patina that is much appreciated by connoisseurs and collectors of fine jewelry. The image (right)shows the finished body, wing and bezel.
The next step is making of the gallery. One of the ways for a collector to quickly determine if a piece of jewelry is of the ultra-fine class is to flip the piece over and examine the back. Traditionally the finest jewelrythe reverse is completely finished. A finely made gallery such as this one, carefully cut out of 18k gold with a jeweler's saw, provides the piece with a finished look but allows the repousee work to be seen. The gallery is fitted to and raised slightly above the reverse of the piece like a sandwich and held in place with each post soldered.
Just before the gem is set, the antenna and feet that have been carefully shaped and fitted are soldered into place. The next image (below) shows a cross section of the piece with the gallery soldered in place.
In our 28 years we have designed and executed over 1,000 custom pieces for our clients.
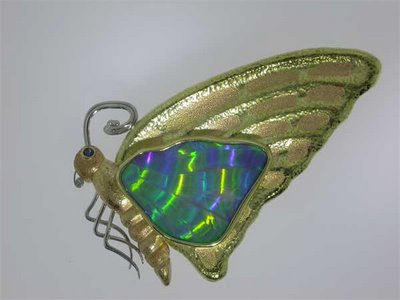
2 comments:
Loved the exposure to such creativity. A nice approach to gemstone/jewelry design.
Great website, very informative, thanks for sharing your jewellers work ,big pats on the back for acknowledging all in the creation of your beautiful pieces.
Post a Comment